Manufacturing: Kit Components Included in Inventory Planning
In previous versions of MYOB Acumatica, companies that used stock or non-stock kits were not able to properly plan the stock components needed to assemble the kit by using the inventory planning functionality. That is, the inventory planning regeneration process did not generate demand requirements for the stock components of a kit when a supply recommendation was made for the kit. When a stock kit was included in a sales order and that kit did not have enough quantity on hand, the user was not alerted to the additional demand for the stock components needed to assemble the kit.
To work around this limitation, users would create a kit assembly document immediately when a sales order for a kit was created. However, in previous versions of MYOB Acumatica, the kit assembly document did not have an allocation date. This resulted in incomplete data being passed to the inventory planning regeneration process, which could not correctly assess when supply and demand were expected.
Additionally, users were unable to use the sales forecast functionality to plan for sales demand for non-stock kits because non-stock kits could not be added to the sales forecast forms.
In MYOB Acumatica 2024.1.1, the inventory planning regeneration process and the sales forecast functionality have been enhanced to address these issues.
- Kit Assembly
- Material Requirements Planning (MRP) or Distribution Requirements Planning (DRP)
Inventory Planning for Stock Kits
Starting in MYOB Acumatica 2024.1.1, the inventory planning functionality now supports the generation of demand requirements for the components of a stock kit that is included in a sales order. The components needed to assemble the kit are now considered planned demand.
For the components of a stock kit to be included in inventory planning, the following criteria must be met:
- On the Stock Items (IN202500) form (Inventory Planning tab), the new Kit Assembly option (which is shown in the following screenshot) is selected in the Source box.
- On the Stock Items form (General tab), MRP or DRP is selected in the Planning Method box.
- On the Kit Specifications (IN209500) form, the kit specification has at least one active revision. If multiple active revisions exist, the most recent one is used for inventory planning.
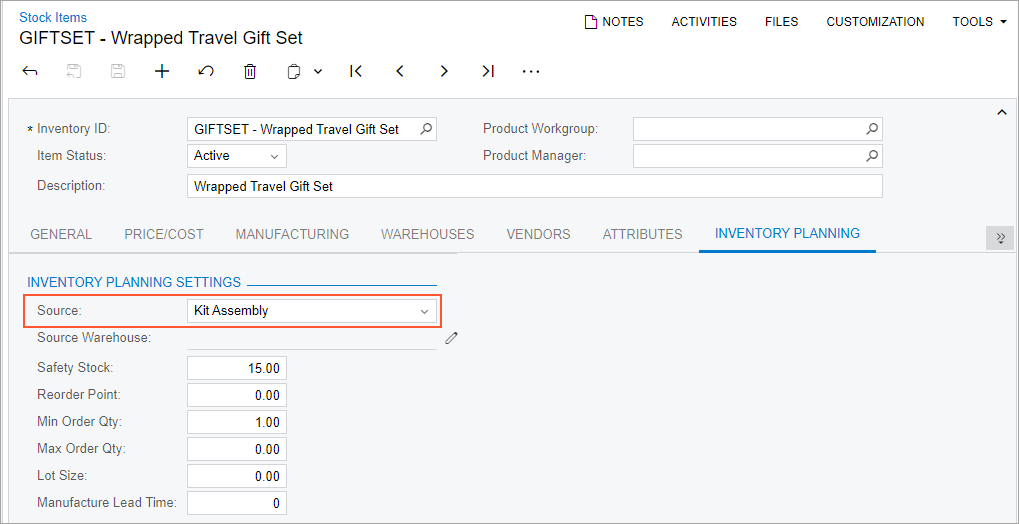
After the inventory planning regeneration process has been run, on the Inventory Planning Display (AM400000) form, the results are displayed for a stock kit with the following settings:
- In the Type column: Planned Kit Assembly Demand. This new type indicates that the demand for the item originates from a system-generated requirement to fulfill a planned kit. (See Item 1 in the following screenshot.)
- In the Related Document column, the identifier of a stock kit planning suggestion. This identifier is generated based on the new numbering sequence, PLSK (Item 2).
- In the new Kit Revision column, the kit specification revision that was used to generate the requirements (Item 3).
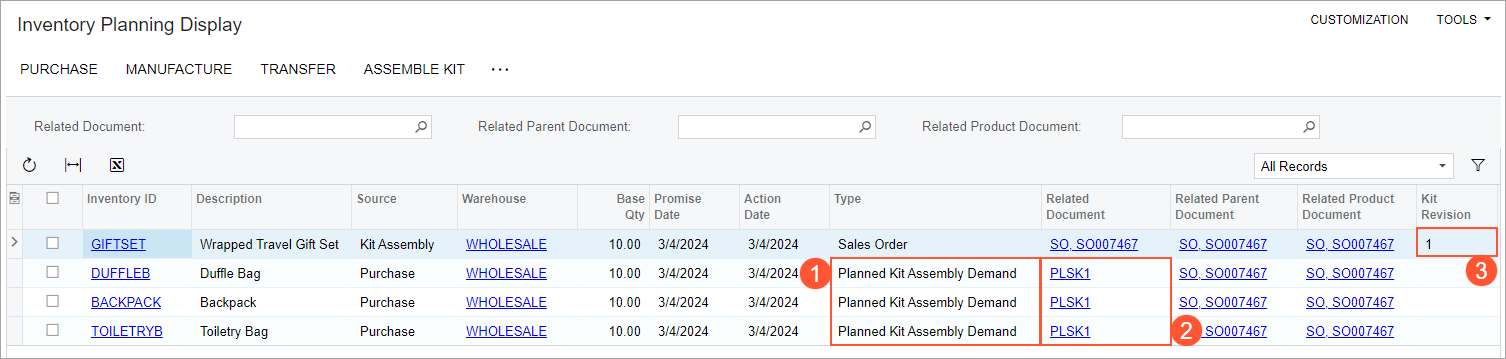
Sales Forecasts and Inventory Planning for Non-Stock Kits
Starting in MYOB Acumatica 2024.1.1, users can generate a forecast for a non-stock kit on the Generate Forecasts (AM502000) form and manually add a forecast record for a non-stock kit on the Forecast (AM202000) form.
The inventory planning process now supports generating requirements for stock components of a non-stock kit that is included in a sales order or a forecast record. The stock components needed to assemble the kit are now considered planned demand.
For the stock components of a non-stock kit to be included in inventory planning, it must meet the following criteria:
- On the Non-Stock Items (IN202500) form (General tab), the Is a Kit check box is selected.
- On the Kit Specifications (IN209500) form, the kit specification has at least one active revision. If multiple active revisions exist, the most recent one is used for inventory planning.
- The non-stock kit is included in a sales order on the Sales Orders (SO301000) form or in a forecast record on the Forecast form.
After the inventory planning regeneration process has been run for a non-stock kit, the Inventory Planning Display (AM400000) form shows the planned suggestions for stock components of the kit. One of the following types is displayed in the Type column (see the following screenshot):
- Sales Order Non-Stock Kit: The demand for the item originates from a sales order line containing a non-stock kit.
- Forecast Non-Stock Kit: The demand for the item originates from a forecast line containing a non-stock kit.
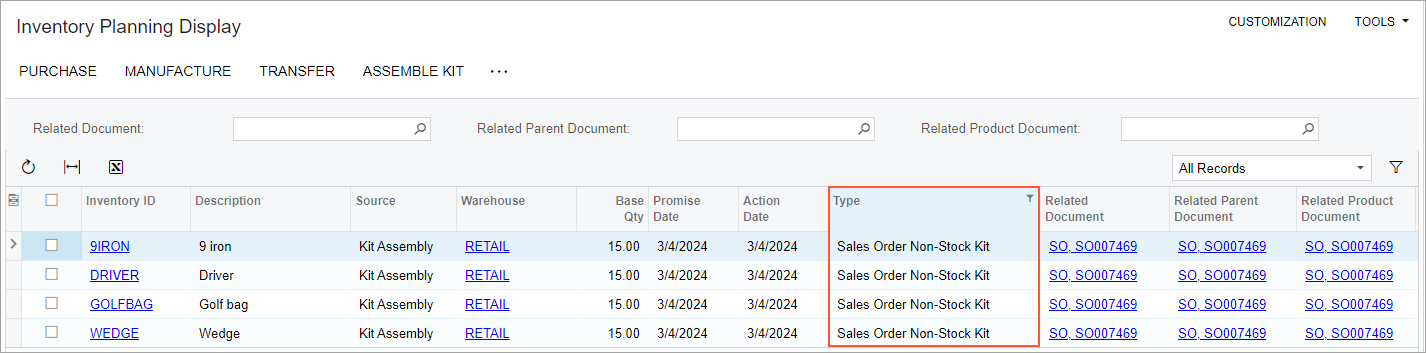
Assembling Kits for Planned Demand
A user can now initiate kit assembly on the Inventory Planning Display (AM400000) form. To do this, they select a row or multiple rows with the Kit Assembly source and click Assemble Kit on the form toolbar. In the Create Kit Assemblies dialog box (which is shown in the following screenshot), the user can group the selected kits and modify their quantities. When the user clicks Create, a kit assembly record is generated on the Kit Assembly (IN307000) form for each processed item.
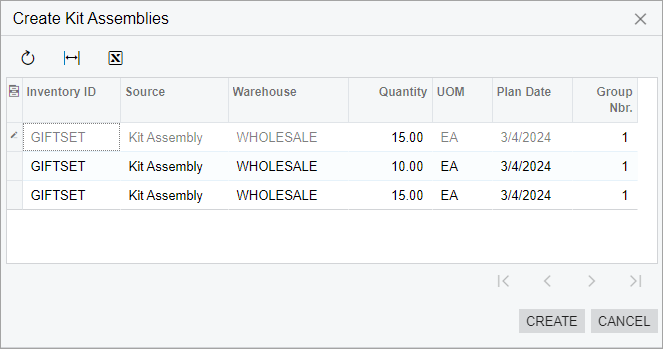
On the Kit Assembly (IN307000) form, kit assembly records are assigned with the Assembly type (previously called Production) and the On Hold status. The system initially populates the kit assembly settings as follows:
- The Inventory ID, Description, Source, Warehouse, and UOM settings are copied from the kit's settings on the Stock Items (IN202500) or Non-Stock Items (IN202000) form.
- The new Requested On box, which is shown in the following screenshot, is filled in with the kit assembly date. A user can modify this date to meet their allocation needs.
- The Location setting of each stock component is copied from the Default Receipt To box on the Item Warehouse Details (IN204500) form.
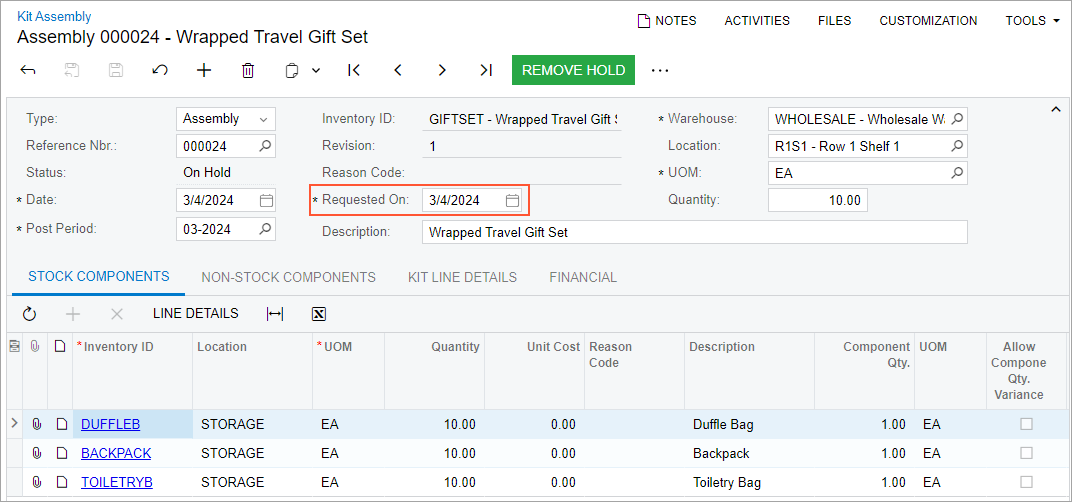
Including On-Hold Kit Assemblies in Inventory Planning
A user can indicate whether to include on-hold kit assemblies in inventory planning. To include kit assemblies with the On Hold status in the regenerate inventory planning process, they select the new Include On-Hold Kit Assemblies check box, which has been added to the General section of the Inventory Planning Preferences (AM100000) form. (See the following screenshot.) When this check box is cleared, kit assemblies with the On Hold status are excluded from the process and are listed as exceptions on the Inventory Planning Exceptions (AM403000) form.
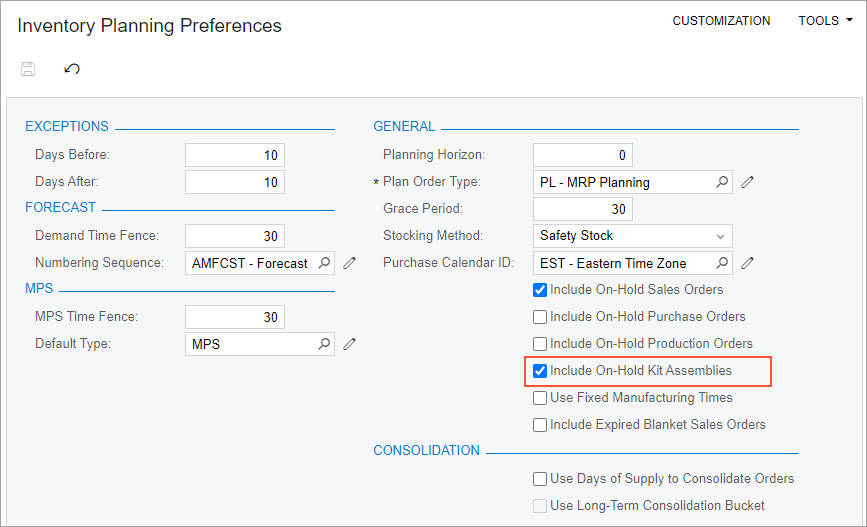