Manufacturing: MRP and Inventory Replenishment Planning Enhancements
To help organizations to maintain proper inventory levels, MYOB Acumatica has two planning processes that it can use to monitor item supply and demand and to then recommend the needed purchases and transfers:
- The inventory replenishment process, which is available if the Inventory Replenishment feature is enabled on the Enable/Disable Features (CS100000) form
- The material requirements planning (MRP) process, which is available when the Material Requirements Planning feature is enabled on the Enable/Disable Features form
In previous versions of MYOB Acumatica, if a company wanted to use the inventory replenishment functionality for some of its inventory and the material requirements planning functionality for their other items in inventory, it was difficult to configure the inventory planning settings because it was unclear which elements affected which planning processes.
In MYOB Acumatica 2024.1.1, users can specify the planning method to be used for a particular item class, stock item, and item–warehouse pair. The ability to specify the record's planning method has been added to the following forms: Item Classes (IN201000), Stock Items (IN202500), and Item Warehouse Details (IN204500).
Also, existing planning elements have been moved and renamed on the above-mentioned forms, as well as on the Warehouses (IN204000) form. These enhancements were designed to improve the user experience and reduce confusion during the configuration of both inventory replenishment planning and material requirements planning.
New Planning Method Box on Multiple Forms
If the Material Requirements Planning and Inventory Replenishment features are both enabled, the new Planning Method box now appears on the Item Classes (IN201000), Stock Items (IN202500), and Item Warehouse Details (IN204500) forms.
This box contains the planning method to be used for the record selected on the form. The planning method specified for the item class is used as the default planning method for stock items created by using that class, but users can change the planning method at the stock item level. The item planning method on the Item Warehouse Details form is informational; MYOB Acumatica Manufacturing Edition does not support different planning methods for different item–warehouse pairs with the same item.
For each item class or stock item, one of the following options should be selected in the Planning Method box of the Item Classes or Stock Items form, respectively:
- None: This option, which is always available, indicates that the stock item should not be planned by using inventory replenishment planning or MRP.
-
Inventory Replenishment: This option is available when the Inventory
Replenishment feature is enabled on the Enable/Disable Features
(CS100000) form. This planning method indicates that the stock item is planned by using
the inventory replenishment planning engine. Only items that are planned by using this
planning engine will appear on the Prepare Replenishment
(IN508000), Calculate Replenishment Parameters (IN508500), and Apply Replenishment Parameters (IN509500) forms. The following screenshot shows
the Inventory Replenishment planning method available for selection on the Stock Items form.
Figure 1. The Inventory Replenishment method on the Stock Items form
- MRP: This option, which is available for selection if the Material
Requirements Planning feature is enabled on the Enable/Disable Features form, indicates that the material requirements
planning engine is used for the item class or the stock item. Only items that are
MRP-planned (that is, items for which this planning method is selected)
will
appear on the following forms:
- Inventory Planning Audit History (AM000017)
- Inventory Planning Buckets (AM201200)
- Inventory Planning Display (AM400000)
- Inventory Planning Exceptions (AM403000)
- Inventory Planning History (AM000016)
- MPS Listing (AM000004)
- Inventory Planning Preferences (AM100000)
- Inventory Planning Requirements by Item (AM401200)
- MPS Type (AM203000)
- Regenerate Inventory Planning (AM505000)
The following screenshot shows the availability of all planning method options on the Stock Items form.
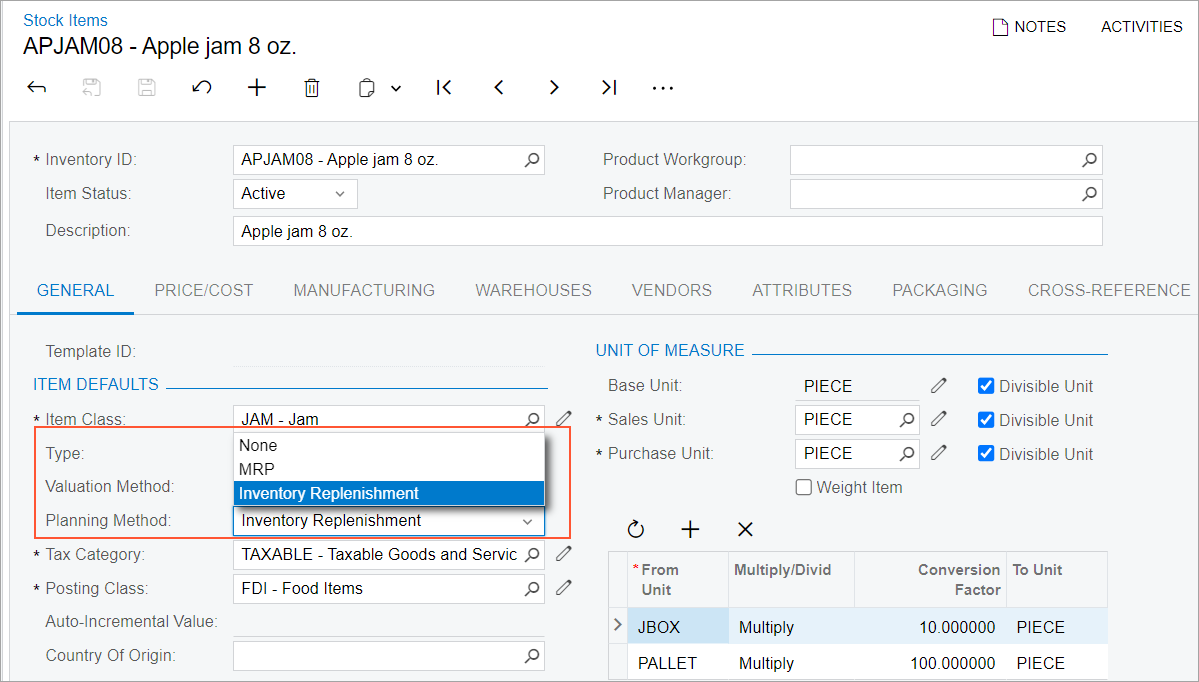
Changes to Forms in the Inventory Workspace
The following table summarizes the changes to the inventory forms.
Form | Difference from the Previous Version |
---|---|
Item Classes (IN201000) Stock Items(IN202500) |
The following differences from the previous version are identical on both the
Item Classes form and the Stock Items form:
|
Item Warehouse Details (IN204500) |
|
Warehouses (IN204000) |
The Inventory Planning tab has been added to the Warehouses form. This tab is displayed when the Material Requirements Planning feature is enabled on the Enable/Disable Features form. The tab contains UI elements that were previously located on the Manufacturing tab. The Inventory Planning tab also includes inventory planning settings that control what supply and demand business documents would be used by the material requirements planning engine. If the Multiple Warehouses feature is enabled on the Enable/Disable Features form, the tab also includes the Transfer Lead Time. |
Prepare Replenishment (IN508000) | This form displays only items for which Inventory Replenishment has been specified as the planning method. |
Calculate Replenishment Parameters (IN508500) | This form displays only items for which Inventory Replenishment has been specified as the planning method. |
Apply Replenishment Parameters (IN509500) | This form displays only items for which Inventory Replenishment has been specified as the planning method. |
Upgrade Notes
If the Inventory Replenishment feature was enabled and the Material Requirements Planning feature was not enabled on the Enable/Disable Features (CS100000) form before the upgrade to MYOB Acumatica 2024.1.1, then the planning method for all stock item classes will be automatically inserted as Inventory Replenishment on the Inventory Planning tab of the Stock Items (IN202500) form.
- For all stock item classes, on the Inventory Planning tab of the Item Classes (IN201000) form and the Stock Items form, respectively, the planning method will be specified as Inventory Replenishment.
- For stock items, the state of the MRP Item check box on the
Manufacturing tab of the Stock Items form determines the planning method to be
inserted in the Planning Method box during upgrade as follows:
- Selected: The planning method will be specified as MRP.
- Cleared: The planning method will be specified as Inventory Replenishment.
If the Material Requirements Planning feature was enabled and Inventory Replenishment feature was disabled before the upgrade, then the following changes occur during the upgrade:
- For all stock item classes, on the Inventory Planning tab of the
Item Classes form, the planning method will be specified
as MRP. Attention: We recommend that you review the settings of stock item classes after the upgrade because new elements are available after the upgrade and default values will be inserted.
- For stock items, the state of the MRP Item check box on the
Manufacturing tab of the Stock Items form determines the planning method to be
inserted during upgrade as follows:
- Selected: The planning method will be specified as MRP.
- Cleared: The planning method will be specified as None.
Additional Information
For more information on MRP, see Configuring Inventory Planning. For more information on inventory replenishment, Configuration of Replenishment: General Information.