Manufacturing: Improvements to Outside Processing and Purchasing Visibility
In MYOB Acumatica 2024.2.1, the process of managing outside services for production operations has been significantly improved. Previously, when a manufacturing company sent manufactured goods to a vendor to perform a service, upon completion of that service a production manager had to manually move the goods from the outside operation to the next operation as a separate step from receiving the purchase order. Users found this manual step redundant and cumbersome. Now the system can be configured to automatically create and release move and material transactions when the purchase orders are received.
Additionally, multiple enhancements have been introduced on the Purchase Orders (PO301000) and Production Order Maintenance (AM201500) forms to improve the visibility of potential links between purchase orders and production orders.
The sections below provide details about the improvements.
Improved Visibility of Production Order Demand in Purchase Orders
In previous versions of MYOB Acumatica, the Purchase Orders (PO301000) form did not indicate whether a purchase was made to fulfill the demand of a production order material. To address this issue, the form has been enhanced to provide visibility into the production order demand linked to each purchase order line.
The View SO Demand button on the table toolbar of the Details tab of the Purchase Orders form has been renamed to View Demand. In the Demand dialog box, which opens when a user clicks this button, information specific to the production order demand is now displayed if the purchase order line is linked to the production order demand, as illustrated in the following screenshot.
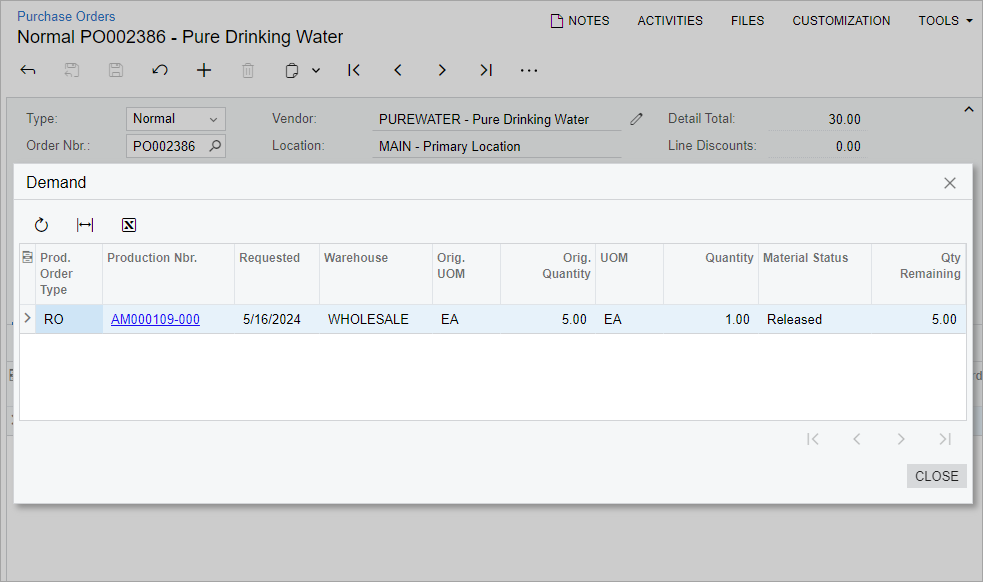
Improved Handling of Outside Processing
On the Materials tab of the Production Order Details (AM209000) form, a new option, Purchase and Move, has been added to the drop-down list in the Subcontract Source column, as shown in the following screenshot. If a purchase order is created for a material line with the Purchase and Move subcontract source selected, the system will automatically create and release a move transaction for the outside operation when a user releases the purchase receipt for the purchase order line. The PO Link button on the table toolbar of the Materials tab is not available when a user selects this material line, which maintains the one-to-one mapping between such material demand lines.
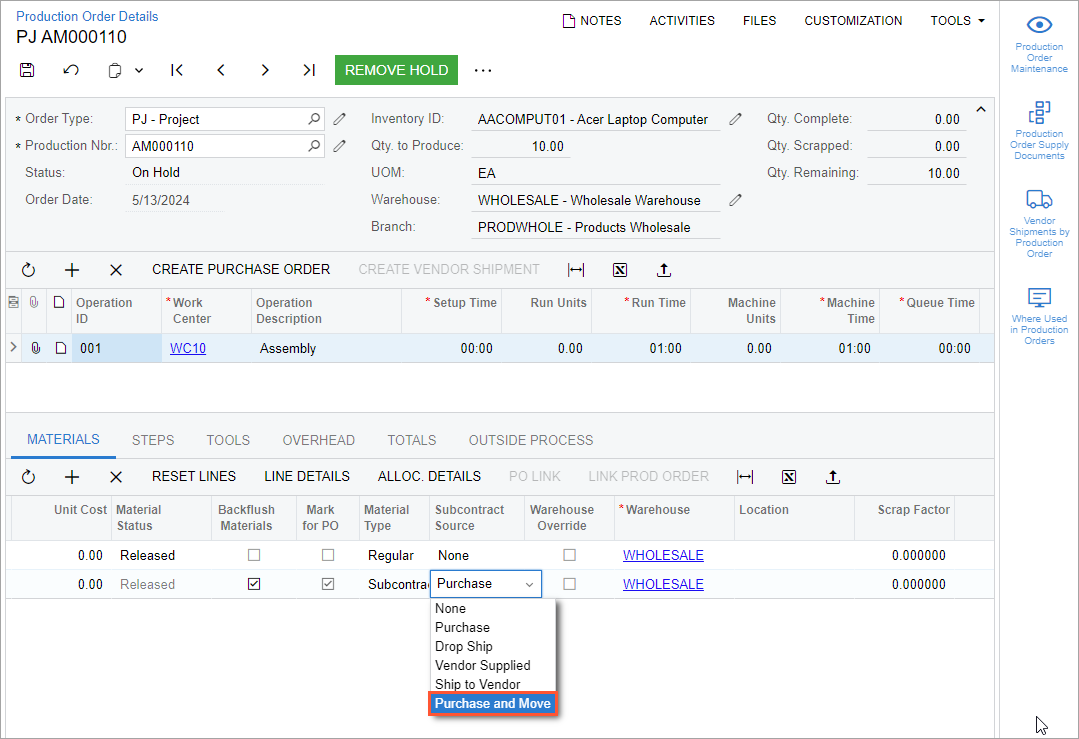
On the Production Order Details, Bill of Material (AM208000), Engineering Change Request (AM210000), Engineering Change Order (AM215000), and Estimate Operation (AM304000) forms, the following applies to material lines with the Subcontract material type and Purchase and Move subcontract source:
- A user can add only one such material line per operation.
- In each of these material lines, the Mark for PO and Backflush Materials check boxes are automatically selected and non-editable.
- To ensure that the Total Required quantity of such a material
line equals Qty to Produce of the outside service operation, the
system inserts the following settings in the line and makes them non-editable:
- Batch Size: 1
- Qty Required: 1
- Scrap Factor: 0
- Qty Round Up: Cleared
When a purchase receipt is released on the Purchase Receipts (PO302000) or Receive and Put Away (PO302020) form, a move transaction is automatically created and released if all of the following conditions are met:
- The purchase receipt has the Receipt type.
- A purchase receipt line is linked to a purchase order line associated with a production order's material line with the Subcontract material type and Purchase and Move subcontract source.
- The status of the linked production order’s material line is Released or In Process.
- The status of the material line's operation is Completed but Warn or Allow is selected in the Move on Completed Operation box on the Production Order Types (AM201100) form for the order type of the linked production order.
- The Qty Remaining of the production order's outside operation equals or exceeds the Receipt Qty of the linked purchase receipt line.
A move transaction with the On Hold status is automatically created on release of a purchase receipt if all of the following conditions are met:
- The purchase receipt has the Receipt type.
- A purchase receipt line is linked to a purchase order line associated with a production order's material line with the Subcontract material type and Purchase and Move subcontract source.
- The Qty Remaining of the production order's outside operation is less than the Receipt Qty of the linked purchase receipt line.
No move transactions will be created automatically if any of the following conditions are met:
- The status of the linked production order’s material line is Canceled, Closed, Completed, or Locked.
- The Release IN Documents Automatically check box on the General tab of the Purchase Orders Preferences (PO101000) form is cleared, and Allow is selected in the Under Issue Backflush Material box on the Production Order Types form for the order type of the linked production order.
A new tab, Move, has been added to the Purchase Receipts form, as shown in the following screenshot. This tab holds information about the automatically generated move transaction.
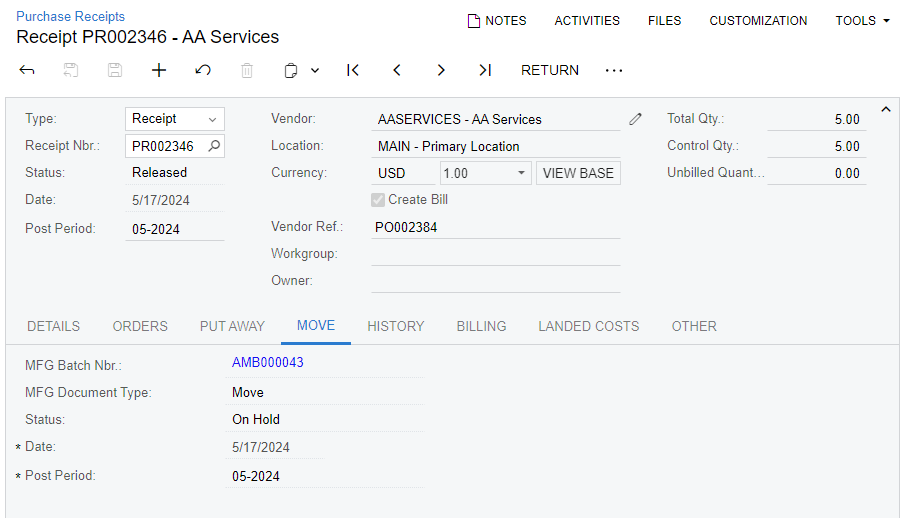
On the Move (AM302000) form, the PO Receipt Nbr. box has been added to the Summary area, as shown in the following screenshot. This non-editable box holds a link to the purchase receipt that produced the move transaction. These links are also displayed in the PO Receipt Nbr. column of the Move (AM3020PL) list of records.
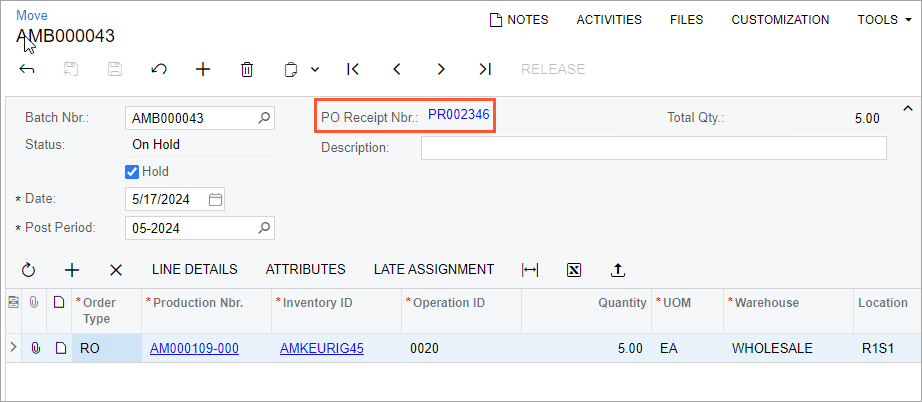
On the Events tab of the Production Order Maintenance (AM201500) form, the system now records events that occur when a linked purchase receipt is released but no move transaction is created and when a move transaction is created but not released.
The system may encounter the following limitations when handling outside services for production operations:
- The automatic release of move transactions will fail upon purchase order receipt if the production order has attributes with the Transaction Required check box selected and a value specified in the Value box on the Attributes tab of the Production Order Maintenance form. This is because the transaction requires manual input of the attribute values, which the automatic process cannot fulfill.
- The system will not create an automatic move transaction for a purchase order created from the Inventory Planning Display (AM400000) form for a material line with the Purchase and Move subcontract source because this form does not support the assignment of purchase orders to production order material lines.
-
If a production order is lot- or serial-tracked and an outside service operation is the last operation on the Production Order Details (AM209000) form, the system will create a move transaction with the On Hold status and will not release it if user intervention is required to enter or select the lot or serial number.
For example, suppose that the Allow Preassigning Lot/Serial Numbers check box is cleared for the production order on the Production Order Maintenance (AM201500) form; also suppose that the User Enterable issue method is selected and the Auto-Generate Next Number check box is cleared for the stock item's lot or serial class on the Lot/Serial Classes (IN207000) form. The system will require the user to manually enter the lot or serial number. In this scenario, the move transaction cannot be automatically released.
To avoid this limitation, the outside service operation should not be set up as the last operation in the production order if the lot or serial class of the stock item has the User Enterable issue method with the automatic number generation disabled and if the lot or serial numbers are not preassigned or involve more than one record.
New Tabs on the Side Panel of the Production Order Maintenance Form
The Production Transactions and Purchase History by Production Order tabs have been added to the side panel of the Production Order Maintenance (AM201500) form, as shown in the following screenshot. By default, these tabs display all production transactions and the purchase history of the selected production order.
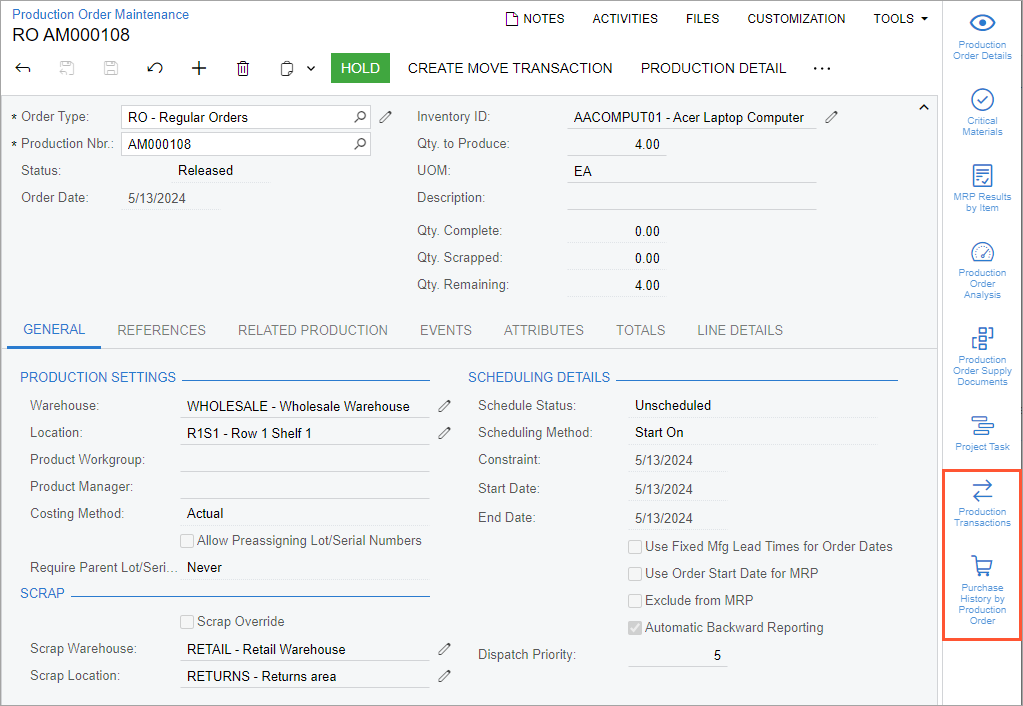
Alignment of Purchase Order Dates with Material Requirements
In previous versions of MYOB Acumatica, if a purchase order was created to fulfill a production order's demand, the system did not use the requested date of the purchase order line, which is specified on the Details tab of the Purchase Orders (PO301000) form, as the start date of the material's operation, although material is required before the linked production order's operation starts.
Now the system uses the requested date of the purchase order line as the allocation date of the production order's material demand, which is also the start date of the material's operation. This happens if the purchase order is created through one of the following ways:
- On the Production Order Details (AM209000) form:
- Through the use of the Create Purchase Orders command on the More menu for the material demand, which opens the Create Purchase Orders (PO305000)
- Through the use of the Create Purchase Order button on the table toolbar of the Operations table for the subcontracting demand, which opens the Create Purchase Orders
- On the Production Order Maintenance (AM201500) form through the use of the Create Purchase Orders command on the More menu
- On the Critical Materials (AM401000) form
When the system aligns the production operation start date to a purchase order it supports only a one-to-one relationship between a purchase order line and the demand of a production order material. It does not support one-to-many, many-to-one, or many-to-many relationships between purchase order lines and production order material demands.
A one-to-one relationship should always be maintained between purchase order lines and production order material demands—that is, one-to-one relationship between demand and supply. If multiple material demands of a production order are linked to a single purchase order line, the system will always use the start date of the first production material's operation as the requested date in the linked purchase order line. This means the system will not consider the start dates of the other production materials' operations, even if they are required at an earlier time.