Returns for Replacement at Another Price: General Information
MYOB Acumatica supports returns of goods for replacement with goods that differ from those that are returned. The returns may include freight, shipping, and handling charges, and the goods may be returned at higher or lower prices. To process such a return, you use a return merchandise authorization (RMA) order, which is an order with the RM predefined order type.
Learning Objectives
In this chapter, you will do the following:
- Become familiar with the general steps involved in the workflow of processing an RMA order
- Create an RMA order
- Process an RMA order
Applicable Scenario
You create a return for replacement at another price (that is, an order of the RM predefined order type) to perform a customer return in which you return an inventory item for replacement. The customer returns the rejected goods, the goods are returned to inventory, and the customer receives a replacement for the rejected goods at another price. For this RMA order, different items than those returned may be included for replacement; freight, shipping, and handling charges may be included, and the replacement items have higher or lower prices than the returned items. Because the items are replaced at a different price, you also need to process AR documents.
General Steps of Returns for Replacement at Another Price
This section describes the general workflow of a return for replacement at another price; for simplicity, a single item is returned and replaced in this workflow.
To process a return of a stock item for replacement at another price, you perform the following general steps:
- On the Sales Orders (SO301000) form, you create a new RMA order.
- Optional:
On
the same form, you add the item to be returned by doing either of the
following:
- You add the stock item to be returned and include a link to the original invoice (that is, the invoice for which the return is being performed) by clicking Add Invoice on the table toolbar of the Details tab and selecting the line of the needed invoice in the Add Invoice Details dialog box, which opens. For the line, notice that by default, the Receipt operation is inserted in the Operation column, and a negative quantity is inserted in the Quantity column.
- You add the stock item to be returned without linking it to an invoice. To do this, you click Add Items on the table toolbar of the Details tab, and select the item in the Inventory Lookup dialog box, which opens. In this case, for the line that has the stock item, you need to specify a negative quantity in the Quantity column. When you do, the option in the Operation column will be changed to Receipt from Issue (the default operation).
Tip:The default operation inserted for a new line on the Details tab of the Sales Orders form is specified on the Templates tab of the Order Types form for the sales order type.After you have added the Receipt lines, make sure that the Auto-Create Issue check box is cleared in these lines (because you need to add replacement items and specify their details manually).
- While you are still on the Sales Orders form, you manually add a line with a positive quantity for the replacement item. Notice that by default, this line has the Issue operation. Each line with the Receipt operation type in an RMA order has a negative quantity, and the corresponding line with the Issue operation type has a positive quantity for a replacement item. Alternatively, if the returned item is not tracked by serial or lot numbers, you can select the Auto-Create Issue check box for the line and manually change the price; on shipment confirmation, the system will add the corresponding lines of the Issue type automatically and copy the line details from the lines of the Receipt type.
- You process the receipt of the returned item and the shipment of the replacement item
(both of which are processed as shipments) by performing the following general
steps
(see Items 4a and 4b in the diagram
below):
- Prepare the receipt (for return) and the shipment (for replacement) by doing the
following on the Sales Orders form:
- To begin preparing the receipt (that is, the incoming shipment with the Receipt operation type), you click Create Receipt on the More menu. You enter the needed settings in the Specify Shipment Parameters dialog box, which opens.
- To begin preparing the outgoing shipment with the Issue operation type, you click Create Shipment on the form toolbar. You then enter the needed settings in the Specify Shipment Parameters dialog box.
You can review the prepared shipments on the Shipments (SO302000) form.
- Confirm the receipt and the shipment.
You can confirm a particular receipt or shipment by selecting it on the Shipments form and clicking Confirm Shipment. When both the receipt and the shipment are confirmed, the original RMA order is assigned the Completed status.
- Prepare the
sales
invoices for the receipt and the
shipment by selecting the document on the Shipments form and
then clicking Prepare Invoice on the More menu.
You can review the prepared documents on the Invoices (SO303000) form. For the return, the system generates an invoice of the Credit Memo type; for the shipment, the system generates a sales invoice of the Invoice type.
Tip:You can print an invoice by clicking Print Invoice, under Printing and Emailing, on the More menu of the Invoices form. - Release the sales invoices. The system automatically generates the following
inventory issues:
- The issue with the Return transaction type for the return
- The issue with the Issue transaction type for replacement
Also, you can review the related AR credit memo and invoice on the Invoices and Memos (AR301000) form.
- Release the generated inventory issues.
The generated inventory issues are released automatically if the Automatically Release IN Documents check box is selected on the Sales Orders Preferences (SO101000) form. If this check box is cleared, you have to release each inventory issue manually by clicking Release on the form toolbar of the Issues (IN302000) form. On release of each inventory issue, a batch of GL transactions is generated.
- Prepare the receipt (for return) and the shipment (for replacement) by doing the
following on the Sales Orders form:
Workflow of a Return for Replacement at Another Price
A general workflow of a return for replacement at another price involves the steps and generated documents shown in the following diagram.
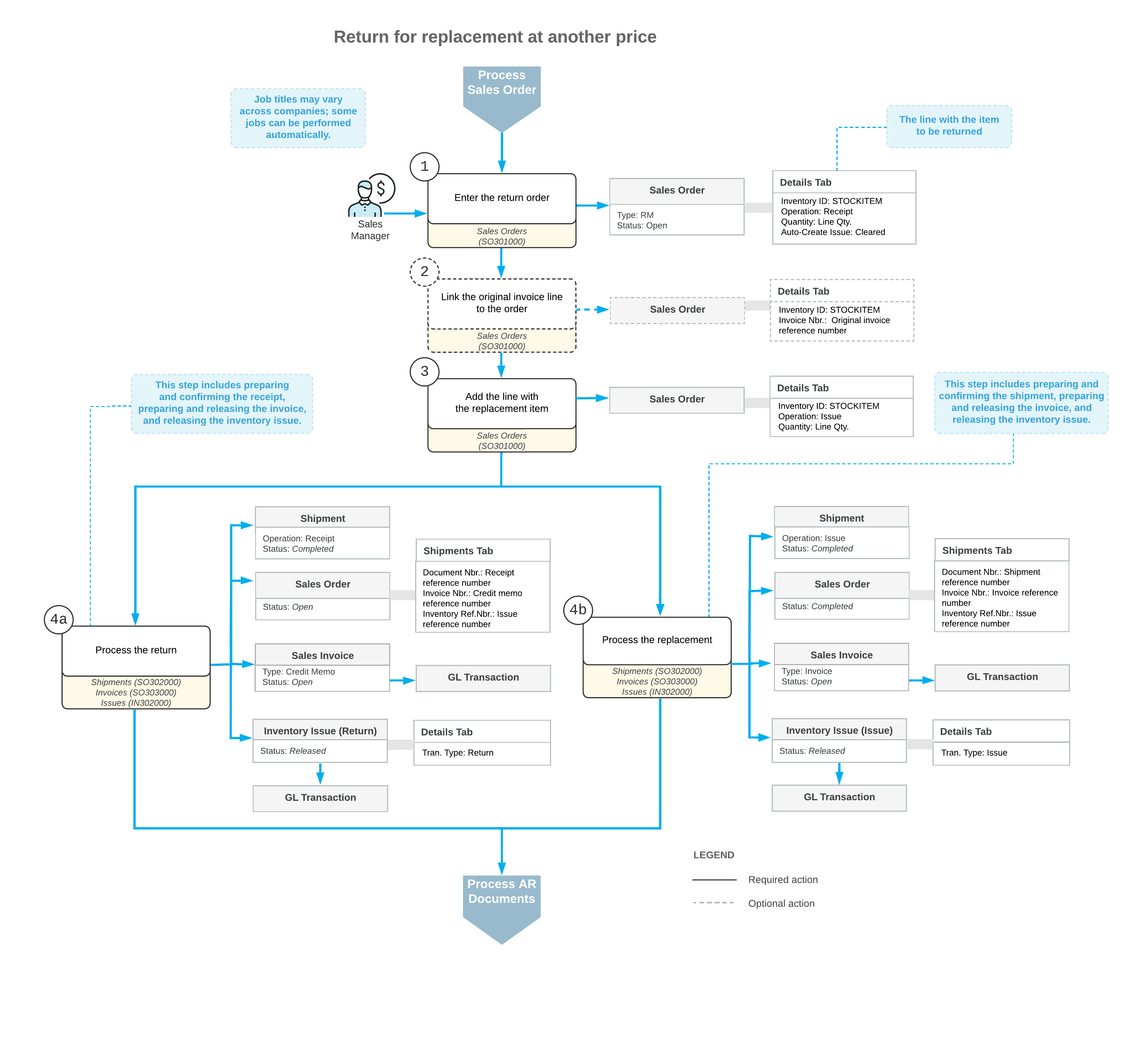