Outside Processing: Processing Workflow
Suppose that you use production orders for tracking outside processing performed by a subcontractor. Further suppose that you have created a non-stock item in MYOB Acumatica Manufacturing Edition for this subcontractor's charges, and you will process vendor shipments in the system when you ship materials to the subcontractor. You have created and released the production order with an outside operation on the Production Order Maintenance (AM201500) form. To process the outside operation, you perform the following general steps:
- Create a purchase order to pay the subcontractor for the services by clicking the
Create Purchase Order button on the Production Order Details (AM209000) form.
The system creates a purchase order on the Purchase Orders (PO301000) form for the vendor specified on the Outside Process tab (if no vendor is specified on the tab, you must specify the vendor manually) and adds items with the Purchase or Purchase and Move subcontract source to the order. The system inserts the purchase order number in the PO Order Nbr. box on the Outside Process tab of the Production Order Details form.
- Create a vendor shipment for the materials required for the outside operation, which are
stored in a warehouse at your facility. You do this by clicking the Create
Vendor Shipment button on the Production Order Details form.
The system creates a vendor shipment for the vendor specified on the Outside Process tab and opens it on the Vendor Shipments (AM310000) form. (If no vendor is specified on the tab, you must specify the vendor manually.) It also adds the following rows to the vendor shipment:
- A row for the item to be produced, which has the WIP type
- A row for each material to be shipped (that is, each item with the Ship to Vendor subcontract source in the production order), which has the Material type
- Optional: Print the pick list by using the Vendor Shipment Pick List (AM644000) report.
- Optional: By using the Vendor Shipment Packing List (AM642000) form, print the packing lists that will accompany the items being sent to the subcontractor.
- On the Vendor Shipments form, confirm the vendor shipment.
For material lines with the Ship to Vendor subcontract source, the system creates the material transaction on the Materials (AM300000) form, issues the materials from the warehouse by creating an inventory issue on the Issues (IN302000) form, and updates the cost in the Subcontractor box of the Actual section on the Totals tab of the Production Order Maintenance form. You can also view the quantity of items shipped to the vendor on the Outside Process tab of the Production Order Details form.
- Create and release a purchase receipt for the purchase order on the Purchase Receipts (PO302000) form.
- Optional: For material lines with the Purchase subcontract source, create and
release a material transaction on the Materials form to apply the
subcontracting costs.
You must perform this step only if the material is not backflushed.
- Optional: For material lines with the Purchase subcontract source, create and
release the move transaction for the outside service operation by using the Move form to record the movement of the items from the outside
operation.
To make the system automatically generate and release the move transaction, you can specify the Purchase and Move subcontract source for the material line.
You then proceed to process the remaining operations in the production order.
The following diagram illustrates the actions and documents that are typically involved in the processing of an outside operation.
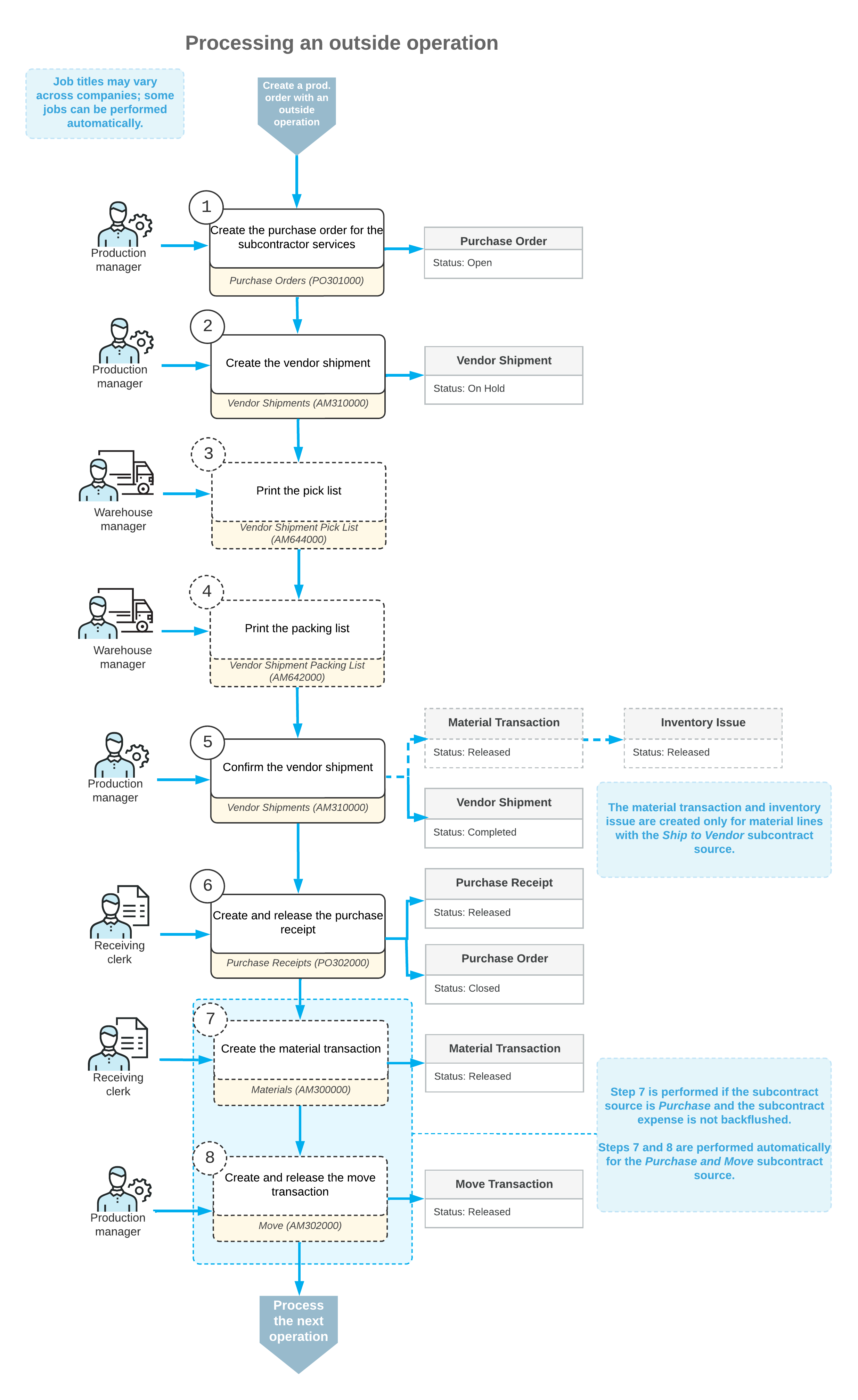