Receiving and Putting Away Operations: Receipt Verification
If the Receiving feature is enabled on the Enable/Disable Features (CS100000) form, during the automated receiving of inventory items, you can perform additional verification of a purchase receipt to ensure the correctness of its items and item quantities. When the Verify Receipts Before Release check box is selected on the Purchase Orders Preferences (PO101000) form, a warehouse worker can no longer release a purchase receipt on the Receive and Put Away (PO302020) form. Instead, the warehouse worker confirms the received quantities, which causes the receipt to be assigned the Received status. Then the warehouse manager (or another user responsible for the verification) verifies and releases the purchase receipt on the Purchase Receipts (PO302000) form.
In this topic, you will read about the workflow for the automated receiving of inventory items with the additional step of purchase receipt verification in MYOB Acumatica. The workflow in this topic is based on the assumption that your system has the recommended configuration described in Receiving and Putting Away Operations: Implementation Checklist.
Workflow for the Automated Receipt of Items with Receipt Verification
The automated processing of receiving items with receipt verification involves the actions shown in the following diagram.
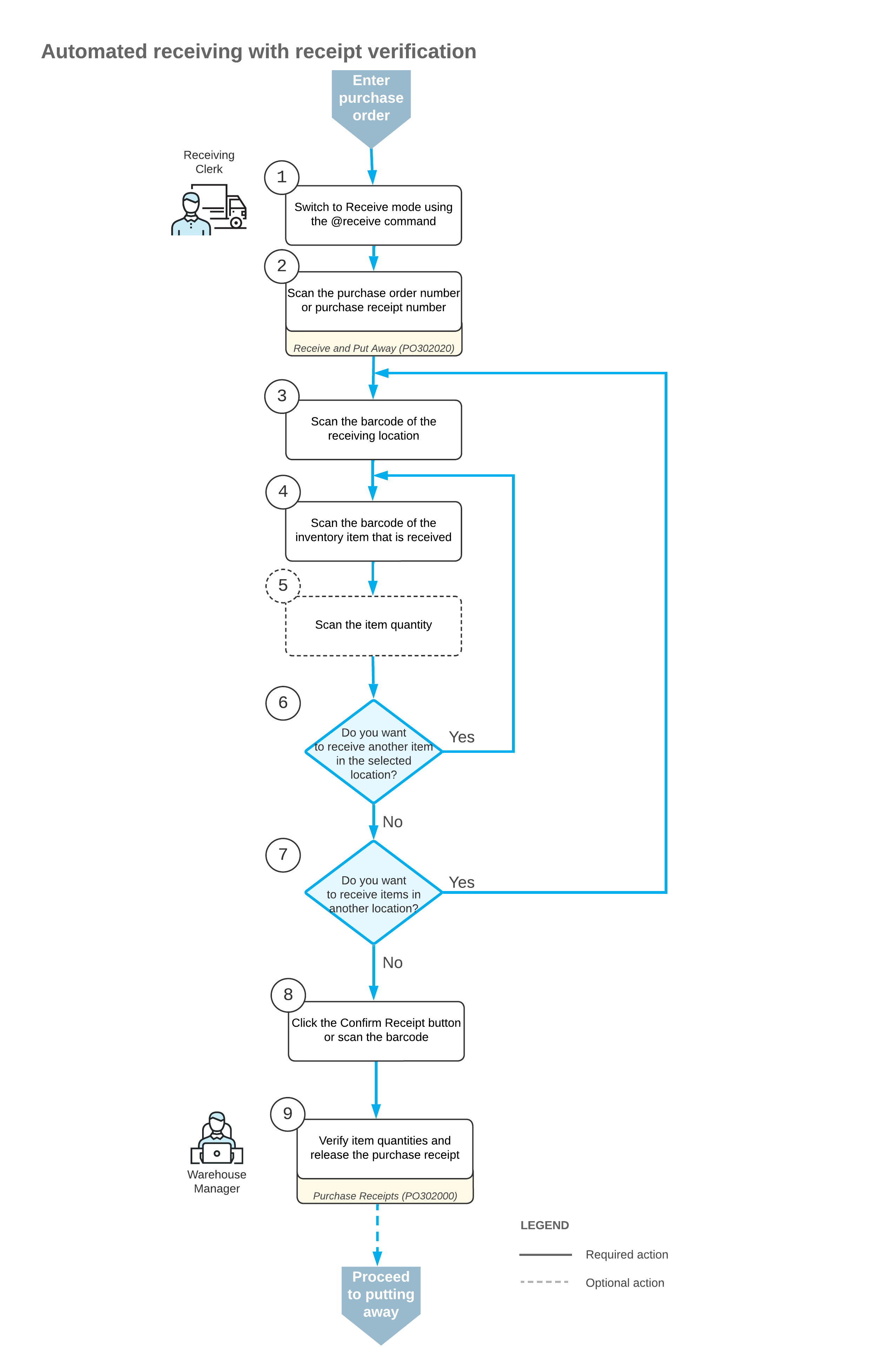
To process the receipt of items (and to use Receive mode), the warehouse employees perform the following steps:
- Warehouse
worker:
Switches
to Receive mode.
They can switch to Receive mode by scanning the @receive barcode.
- Warehouse worker:
Scans
the document number.
To start the automated processing, they scan the reference number of the purchase order, purchase receipt, or purchase return document to be processed. (They use Return mode to process a purchase return.) The system displays the lines of the scanned document in the table of the Receive and Put Away (PO302020) form. If they have scanned the purchase order number, the system creates and saves the related purchase receipt automatically. In the Receipt Nbr. box, the system inserts the reference number of the receipt or return that is currently selected for processing.
Tip: If the purchase order has 15 or fewer lines, the system creates the related purchase receipt and adds the lines of the order to the receipt automatically. If the purchase order has more than 15 lines, the created purchase receipt does not have any lines. The receipt lines are added when they scan the barcodes of the items of the purchase order. - Warehouse worker:
Scans
the barcode of the receiving location.
They scan the barcode of the warehouse location where the items are being received.
- Warehouse worker:
Scans
the item barcode.
When they scan the barcode of the received item, the system searches for the item in the lines of the document that is currently selected. If the item is found, the system highlights the line in bold.
- Warehouse worker:
Scans
the item quantity (optional).
To change the received quantity in the line that is currently being processed, they switch on Quantity Editing mode by scanning or entering the *qty barcode, and manually enter the quantity in the UOM defined by the barcode of the scanned item.
Tip: The system updates the quantity of the item in the purchase receipt on the Purchase Receipts (PO302000) form only after they release this purchase receipt on the Receive and Put Away form. If the received quantity of the item on the Receive and Put Away form differs from the quantity of the item on the Purchase Receipts form, they need to verify if the purchase receipt is released on the Receive and Put Away form. - Warehouse worker:
Receives
another item.
If they need to receive at least one other item for the document currently being processed, they return to scanning the item barcode (that is, return to Step 4) and repeat the process for the item.
- Warehouse worker:
Receives
items in another location.
If items must be received in another warehouse location, they scan the barcode of this location (return to Step 3) and repeat the process for the next location.
- Warehouse worker:
Completes
the receiving process.
If they have finished the receiving operation and all items have been received for the purchase receipt, they scan the *confirm*receipt barcode or click the Confirm Receipt button. The system does not mark partially received lines as completed and assigns the Received status to the purchase receipt on the Purchase Receipts form.
- Warehouse manager: Verifies the receipt.
They open the receipt on the Purchase Receipts form, check items and item quantities, correct any mistakes, and release the receipt.