Project Material Management: General Information
As a project progresses, the company purchases materials and services that are then used to complete the work related to the project. As such, these materials and services should be carefully reflected in the project cost budget. Effective material management and proper financial tracking of project materials are essential for controlling project costs and ensuring that the project costs are aligned with the approved budget.
The topics of this chapter describe the overall flow of project material management and provide recommendations on how you should configure inventory items to be used in projects and how you can record expenses to particular accounts and subaccounts related to projects or project tasks. Also, these topics explain how these expenses are recorded to project budget.
Learning Objectives
In this chapter, you will learn how to do the following:
- Configure reason codes to be used for project-related inventory transactions
- Configure posting classes for project-related stock
- Process project-related documents with inventory items
- Record the cost of items to the project budget
Applicable Scenarios
You need to accurately track materials and services purchased for projects to avoid delays, minimize costs, and ensure the availability of necessary resources at each stage of the project.
Material Management in Construction Projects
Throughout a project's lifecycle, the company manages inventory, tracks the usage of materials, and ensures that materials and services are utilized efficiently. This involves regular communication with vendors and subcontractors, continuous monitoring of supply levels, and adjustments to procurement strategies as the project evolves. You need proper documentation and financial tracking to maintain transparency and control over project costs, ensuring that expenditures are aligned with the approved budget.
The process of managing the materials and services required for construction projects typically consists of the following general stages:
- Take-off stage: This stage includes confirmation of the project scope with the customer, identification of the specific materials and services required based on detailed project plans and specifications, and general measurement of required materials and services.
- Budget preparation: Based on the results of the take-off stage, the project manager estimates the overall amount of required materials and services and prepares the project budget. In the cost budget of the project, the original budgeted values are specified.
- Purchase planning: The project manager decides how the materials and services will be purchased based on the project schedule, required resources, and availability of particular items on the vendor side.
- Buyout: Once the requirements are clearly defined, the project manager initiates a search of vendors and subcontractors, evaluating potential suppliers based on various important factors that should be aligned with the project’s timeframes. These key factors include the price of materials or services, item quality, and estimated delivery times, which should be aligned with the project's timeframes.
- Commitment: After selecting the vendors, the purchasing manager places purchase orders and
subcontracts, specifying the quantities, delivery schedules, and other important details
aligned with the project goals. As the result, in the cost budget of the project, the committed
values are specified. Important: For accurate tracking of project costs, we recommend that you use the commitment tracking functionality. For more information, see Committed Costs: General Information.
Purchase and Issue of Materials
Depending on a company’s business processes, the following general cases of utilizing materials for projects are possible:
- The materials are purchased and drop-shipped directly to the project site. In this case, the purchasing manager creates orders of the Project Drop-Ship type on the Purchase Orders (PO301000) form. When a purchase order is removed from hold, the system creates a commitment to the project budget. Actual costs are recorded to the project budget on release of the AP bill for the project drop-ship order.
- The materials are purchased and reserved for a particular project. These materials are
stored in a company yard (warehouse) until they are issued for the project. In this scenario,
the purchasing manager creates purchase orders of the Normal type on the Purchase Orders (PO301000) form. When a purchase order is removed from hold, the
system creates a commitment to the project budget. Actual costs are recorded to the project
budget on release of the AP bill for the purchase order.Important: Retail drop shipment orders (that is, purchase orders of the Drop-Ship type) are not intended for use with projects.
- The materials are provided by a subcontractor along with services related to these materials. In this scenario, the purchasing manager creates subcontracts on the Subcontracts (SC301000) form. When a subcontract is removed from hold, the system creates a commitment to the project budget. Actual costs are recorded to the project budget on release of the AP bill for the subcontract.
- The materials are already available at a company warehouse as a free stock, which is not reserved for any project. In this case, the project manager issues the stock directly for the project on the Issues (IN302000) form. These materials will be recorded as actual expenses on release of the inventory issue transaction. The system does not track these materials as project commitments. Actual costs are recorded to the project budget on release of the inventory issue.
The following diagram illustrates the material management flow in projects and shows how costs are recorded to the project budget depending on the type of document being processed.
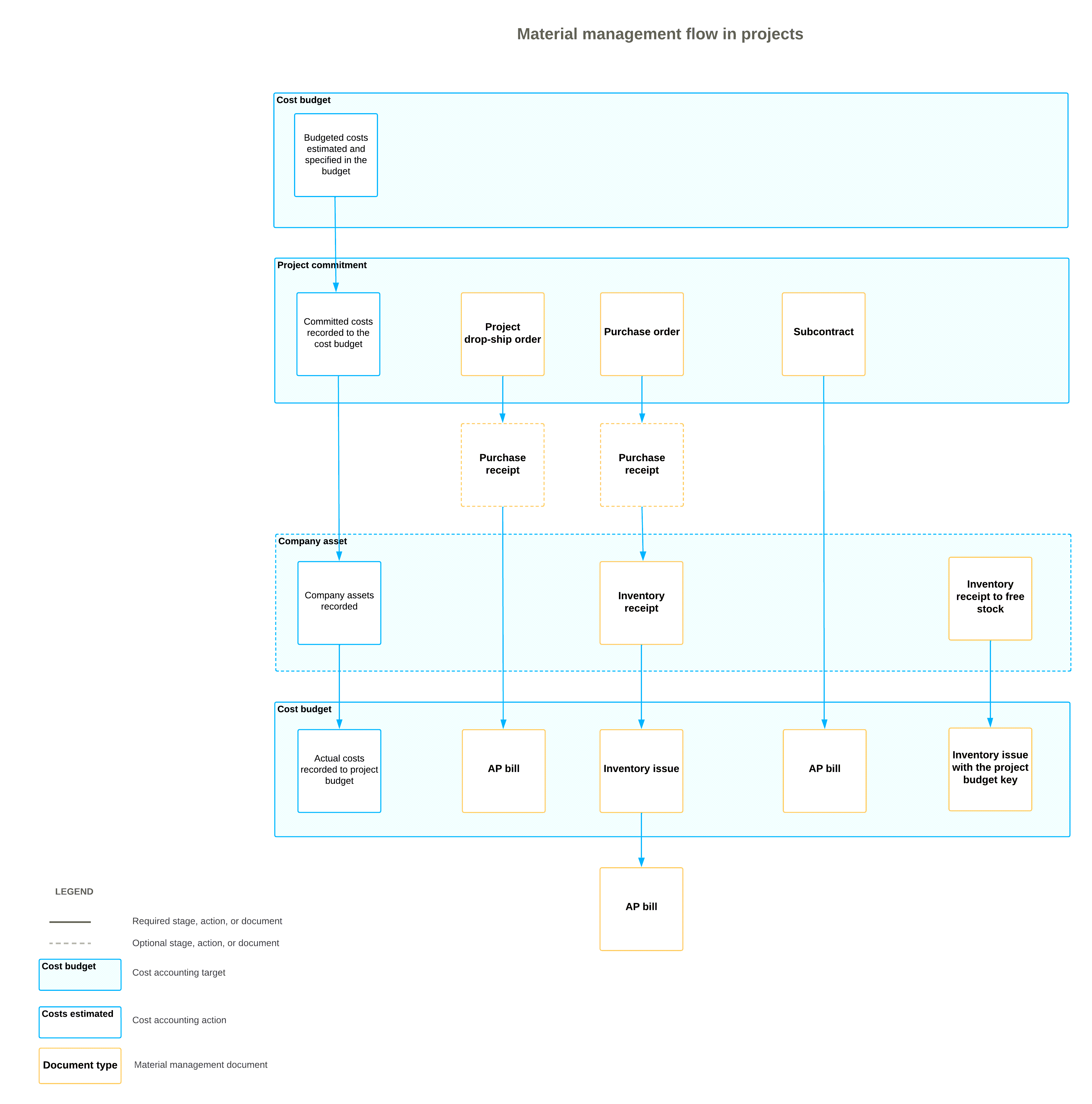
If some project inventory is left unused for a completed project, you need to transfer all the leftover material back to the free stock. For more information, see Project Inventory Tracking: Mass Processing.